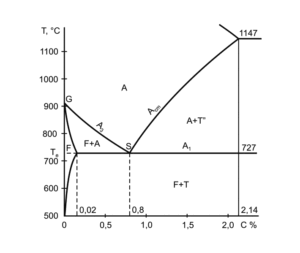
Termotöötlus (heat treatment) on kasutatavam tootmisprotsess, mis toote kuju muutmata võimaldab muuta nii materjali füüsikalisi kui ka mehaanilisi omadusi, nagu tugevus, sitkus, töödeldavus, kulumiskindlus ja korrosioonikindlus. Terase termotöötluse, nii nagu igasuguse termotöötluse, eesmärgiks on metalli omaduste muutmine struktuuri muutmise teel ja see seisneb uumutamises, seisutamises etteantud temperatuuril ja jahutamises. Terase struktuuris oleva austeniidi lagunemisel tekkivate struktuuride mitmekesisus teeb võimalikuks teraste omaduste laia varieerumise nende termotöötlusel. Termotöötlusega võib muuta nii terase mehaanilisi, tehnoloogilisi kui ka talitusomadusi. Faasidiagrammil (pildike parmal) on ära toodud võtmefaasimuutuste jooned.
- Joon A1 on eutektoidmuutuse joon
- Joon A3 on austeniidi ja feriidi-austeniidi alade vaheliseks piiriks
- Joon Acm iseloomustab tsementiidi teket austeniidist (eralduspiir austeniidi ja austeniidi-tsementiidi alade vahel)
Toetudes eelpooltoodule on siis terase termotöötluse põhimoodusteks lõõmutus, normalisatsioon, karastus ja noolutus. Eraldi grupid moodustavad termokeemiline ja termomehaaniline töötlus.
Lõõmutamine
Lõõmutamine (annealing) on termotöötluse protsess, kus terast kuumutatakse üle faasimuutuste temperatuuride A1, A3, Acm järgneva aeglase jahutamisega. Tavaliselt on seda mõistlik teha ahjus. Lõõmutus on üldiselt esmane termotöötlemise viis, mille eesmärgiks on kas kõrvaldada kuumtöötluse eelmiste operatsioonide (valamise, sepistamise jms) defekte või valmistada struktuuri ette järgnevateks operatsioonideks (näiteks lõiketöötlemiseks või karastamiseks). Üsna sageli on aga lõõmutamine lõplik termotöötlemise operatsioon ja seda siis, kui lõõmutatud terase mehaanilised omadused rahuldavad, s.t pole vaja edaspidist parendamist (karastamist ja noolutamist). Lõõmutuse peamine eesmärk on vajalike omaduste tagamine terase ümberkristalliseerimise ja sisepingete kaotamise tagajärjel. Lõõmutamise erisused on siis difusioonlõõmutus, täis- ehk tavalõõmutus, madallõõmutus.
Täislõõmutuse (full annealing, true annealing) eesmärk on sepiste ja valandite struktuuri peenendamine ning sisepingete kaotamine. Alaeutektoidteraste korral kuumutatakse täislõõmutamisel terast üle faasipiiri A3, millele järgneb aeglane jahutamine. Alaeutektoidterase ferriitperliitstruktuur muutub kuumutamisel austeniidiks ning jahutamisel tekib ümberkristalliseerumisel austeniidist uuesti ferriit ja hõrelamelne perliit. Sellise termotöötluse tulemusena saadakse sageli valamisel ja sepistamisel tekkinud jämeteralisest ferriitperliitstruktuurist peeneteralisem ferriitperliitstruktuur. Terase kuumutamisel üle faasipiiri A3 tekivad perliidis kõigepealt peened austeniidi kristallisatsioonikeskmed, mis vastavalt temperatuuri tõusule järjest kasvavad. Kui temperatuuri tõsta ainult 30…50 °C üle A3 ja hoida sepist või valandit sellel temperatuuril, siis ei kasva austeniiditera suureks. Jahutades nüüd terast vähemalt 30 °C allapoole faasipiiri A1, saame ühtlase ja peeneteralise ferriitperliitstruktuuri. Seejuures moodustub austeniiditera sees mitu perliiditera, mis on tunduvalt väiksemad kui austeniiditera, millest nad tekkisid. Alaeutektoidteraste lõõmutamisel üle faasipiiri A1, kuid alla A3 – poollõõmutusel (non-full annealing) pürgivad perliidis olevad tsementiidiosakesed sferoidiseeruma. Lõõmutusaega reguleerides on võimalik saada struktuur, kus osa tsementiiti on muutunud terajaks, s.t struktuur pole pehmenenud kogu ulatuses. Sagedamini kasutatakse aga eespool vaadeldud täislõõmutuse asemel termotöötlust, mis seisneb kuumutamises üle A3 ja kiires allajahutamises 500…600 °C-ni edasise aeglase jahutamisega toatemperatuurini. Teraja struktuuri saamiseks võib täislõõmutusel kasutada ka lühiajalist, terajate karbiidide teket soodustavat seisutust temperatuurist A1 veidi allpool. Suurema süsinikusisaldusega terase (0,5 % ja enam) kuumtöötlemise ja ka normaliseerimise tulemusena moodustub struktuur, mis on liiga kõva nii külm- kui ka lõiketöötlemiseks. Nimetatud juhtudel ja teraste korral kasutatakse madalamatemperatuursemat lõõmutust – terast kuumutatakse tavaliselt üle faasipiiri A1, millele järgneb aeglane jahutus. Selle tulemusena saadakse üleeutektoidteraste struktuuris terajad (sferoidaalsed) tsementiidiosakesed. Eriti oluline on selliste karbiidiosakestega struktuur kiirlõike- ja kõrglegeerteraste korral. Täislõõmutust kasutatakse kõrgsüsinikteraste (üleeutektoidteraste) sisepingete kaotamiseks, kõvaduse vähendamiseks, plastsuse suurendamiseks ja lõiketöödeldavuse parandamiseks. Üleeutektoidteraste täislõõmutust nimetatakse ka sferoidiseerivaks lõõmutuseks ehk sferoidisatsiooniks (spheroidizing annealing, spheroidization), ja see on teraja tsementiidiga sferoidaalse struktuuri saamise põhiline viis. Selline struktuur tekib ainult juhul, kui kuumutada üle faasipiiri A1 (740…800 °C, 2…4 h) (kõrgem lõõmutustemperatuur põhjustab lamellperliidi teket). Kuumutamisele järgneb aeglane jahutamine ahjus (ca 20 °C/h) kuni temperatuurini 600 °C, edasi toatemperatuurini juba õhus. Aeglase jahtumise käigus eraldub terajas tsementiit, mis takistab lamellperliidi teket. Lõõmutatud terase struktuur koosneb teraperliidist ehk sferoidiidist (globular pearlite, spheroidite) – ferriidi põhimassist ja teralisest tsementiidist. Vaadeldud üleeutektoidterase sferoidiseerivat lõõmutust reguleeritakse kuumutustemperatuuri, -aja ja jahutuskiirusega. Madala kuumutustemperatuuri puhul muutub sferoidiseerimisprotsess liiga pikaks; liiga kõrge kuumutustemperatuur põhjustab tsementiidi täieliku eraldumise austeniidist, mis hilisemal jahutamisel soodustab lamellperliidi teket. Sama tulemus on ka siis, kui jahtumiskiirus kuni temperatuurini 600 °C on liiga suur. Seega saab jahtumiskiiruse valikuga reguleerida tekkivat struktuuri (tsementiidiosakeste kuju ja disperssust) ja nii mõjutada terase kõvadust ja teisi omadusi. Tööriistaterase teraline struktuur tagab selle hea lõiketöödeldavuse ja karastamisel väikese kalduvuse ülekuumenemisele (terakasvule). Kuumutades terast üle Acm täisausteniitsesse alasse, tekib aeglasel jahutamisel tsementiidivõrk terapiiridel, mis teeb terase hapraks.
Madallõõmutust kasutatakse siis, kui erinevate töötluste tulemusel jäävad detailidesse pinged, mis on tingitud nende eri osades esinevatest plastsetest deformatsioonidest. Makropinged (macroscopic stresses) tekivad külmtöötlusel, s.t kalestumisest plastsel töötlusel. Termopinged (thermal stresses) tekivad temperatuuri erinevuste tõttu detaili eri osade vahel, tavaliselt aga valandite ja keevisõmbluste kiirel jahutamisel, faasipinged (phase stresses) aga faasimuutustest. Kõik seda liiki sisepinged avaldavad mõju detaili omadustele. Üldjuhul on need ebasoovitavad, kutsudes esile purunemisi, mis on avariide põhjuseks. Seetõttu püütakse selliste sisepingete tekkimist vältida. Nende tekke ja olemasolu korral tuleks detaile täiendavalt termotöödelda. Selleks sobib madallõõmutus ehk madalatemperatuurne lõõmutus (nimetatakse ka pingetuslõõmutuseks) (stress relief annealing, low-temperature annealing). Kuna sellise lõõmutamise peaeesmärk on terase kõvaduse vähendamine ja plastsuse suurendamine, siis nimetatakse seda ka pehmelõõmutuseks (soft annealing). Sellist lõõmutust kasutatakse tavaliselt siis, kui terase algstruktuur on sobiv ja puudub vajadus faasilise ümberkristalliseerimisega lõõmutuse järele. Terast madallõõmutatakse allpool faasipiiri A1, tavaliselt temperatuuril 500…650 °C ja jahutatakse seejärel aeglaselt, tavaliselt ahjus. Sisepinged alanevad pikaajalise lõõmu tuse tagajärjel ja seda põhjalikumalt, mida kõrgemal temperatuuril lõõmutus toimub. Temperatuuridel üle 650 °C täheldatakse perliidi sferoidiseerumist ja terase pehmenemist; kuumutamisel üle faasipiiri A1 leiavad aset faasimuutused ja tekivad struktuurid kooskõlas Fe-Fe3C faasidiagrammiga (p 3.5.2). Aeglane jahutus on vajalik selleks, et ei tekiks jahtumisest tingitud termopingeid. Nii peaks paksuseinaliste valandite korral normaliseerimisele järgnema madallõõmutus, mida, tõsi küll, võib ka ühitada normaliseerimisega. Viimasel juhul jahutatakse valandit aeglaselt temperatuurist 650…600 °C allpool, kusjuures säilib struktuur, millele püüeldakse normaliseerimisel. Selleks paigutatakse valand normaliseerimistemperatuurilt ahju, mis on eelnevalt kuumutatud temperatuurini 600…650 °C, jahutades seejärel valandit termopingete vältimiseks ahjus temperatuurini 200 °C. Oluline on teada, et termopinged võivad tekkida ka suurte ja paksuseinaliste detailide kiire ja ebaühtlase kuumutamise tagajärjel. See oht on suur eriteraste ja -sulamite korral, mille soojusjuhtivus on väike – tekib suur temperatuuride erinevus detaili eri osade vahel. Siit tulenevalt kuumutatakse sellistest terastest suuri detaile aeglaselt temperatuurini 600 °C, et vähendada kuumutamisel tekkivaid termopingeid. See võimaldab vältida detailide ebaühtlasest kuumutamisest tingitud purunemisi. Madallõõmutuse üks liik on rekristalliseeriv lõõmutus ehk rekristallisatsioonilõõmutus (recrystallization annealing), mida kasutatakse eelneva plastse külmdeformatsiooni tagajärjel tekkinud kalestuse kõrvaldamiseks. Rekristallisatsioonilõõmutamisel kuumutatakse terast faasipiirist A1 veidi madalamate temperatuurideni (kuni 650…700 °C), seisutatakse sellel temperatuuril ja jahutatakse seejärel aeglaselt. Selle tulemusena toimub metalli sekundaarne kristalliseerumine – rekristallisatsioon (recrystallization) (vt p 2.2.4). Deformeeritud terade piiridel tekivad uued kristallisatsioonikeskmed, millest moodustuvad uued terad. Vanade deformeerunud terade asemele tekivad uued võrdtelgsed terad ning deformeerunud struktuur kaob. Selle tulemusena taastub metalli esialgne struktuur. Ferriidi rekristalliseerumise (taastumise) tulemuseks võib olla üsna suur tera, kui terase lõõmutusele on eelnenud plastne deformatsioon 5…15 % piires, s.o nn kriitiline deformatsiooniaste (critical deformation step). Seega tuleb peeneteralise struktuuri saamiseks vältida nimetatud deformatsiooniastmeid. See on ka põhjus, miks rekristallisatsiooniprotsessi kiirendamiseks ei saa rekristallisatsioonilõõmutust asendada normaliseerimisega, eriti madalsüsinikteraste korral, ehkki mõlemad viivad terase kõvaduse vähenemisele. Rekristallisatsioonilõõmutuse võib asendada normaliseerimisega juhul, kui tegemist pole kriitiliste deformatsiooniastmetega. Peab silmas pidama, et eriti hädaohtlik on struktuuri jämeteralisus ferriitterastes (ferriitstruktuur esineb kogu temperatuurivahemikus – toatemperatuurist kuni solidusjooneni), kuna kõrgetel temperatuuridel moodustunud jäme tera ei peenene ka termotöötluse tulemusel. Rekristallisatsioonilõõmutust kasutatakse märkimisväärse osa teraste sortimendi, s.o külmvaltsteraspleki korral (ca 15 % kõigist toodetavaist terastest), aga ka kuumvaltsitud ja tõmmatud teraste korral, kui protsessi lõpptemperatuur on 600 °C piires.
Difusioonlõõmutust (diffusion annealing, homogenizing) kasutatakse eelkõige legeerterasest valuplokkide ja valandite keemilise koostise ühtlustamiseks. Koostise ebaühtlust põhjustab eelkõige karbiidne ja dendriitne likvatsioon, mis on tingitud legeerivate elementide kuhjumisest karbiidide kristallisatsioonikeskmeisse ja dendriitide keskossa. Keemilise koostise ühtlustamiseks kuumutatakse valuplokke või valandeid kõrgete temperatuurideni, mille juures keemiliste elementide aatomite liikuvus (difusioonikiirus) on suur. Selle tulemusel paigutuvad aatomid neist kohtadest, kus kontsentratsioon on suurem, kohtadesse, kus kontsentratsioon on väiksem – leiavad aset difusiooniprotsessid. Sellise difusiooni tulemusena ühtlustub valuploki või valandi keemiline koostis. Et tagada aatomite vajalikku difusioonikiirust, lõõmutatakse teraseid temperatuuril kuni 1100 °C, seisutusaeg 10…20 h. Kuumutus temperatuurideni 1000…1100 °C ja pikaajaline seisutus sellel põhjustavad austeniiditera tunduvat kasvamist – struktuur muutub jämeteraliseks. Samuti väheneb pärast sellist termotöötlust erinevus üksikute terade keemilises koostises. Seetõttu on nõutav täiendav termotöötluse operatsioon struktuuri peenendamiseks (täis- või poollõõmutus). Normalisatsioon Kuigi terase täislõõmutus tagab meile hea plastsuse ja väikese tugevuse, on see aega ja energiat nõudev. Kui pole olulised eespool esitatud omadused, tähtis on aga hind, kasutatakse normaliseerimist.
Normaliseerimine
Normalisatsioon ehk normaliseerimine (normalization, normalizing) on selline termotöötluse viis, mille korral terast kuumutatakse 30…50 °C üle vastavate faasipiiride – alaeutektoidteraseid üle A3, üleeutektoidteraseid üle Acm, seisutatakse sellel temperatuuril ja jahutatakse siis õhus. Normaliseerimise tulemusel vähenevad sisepinged ja toimub terase faasiline ümberkristalliseerumine, mis muudab valandite, sepiste ja keevisõmbluste jämeteralise struktuuri peeneteralisemaks. Normaliseerimine on lõõmutamisega võrreldes odavam termotöötluse moodus, sest ahju kasutatakse ainult kuumutamiseks ja seisutamiseks antud temperatuuril, jahutamine toimub juba õhus. Lõõmutatud ja normaliseeritud madalsüsinik- ja madallegeerteraste omadustel pole olulist vahet, mistõttu neid teraseid soovitatakse lõõmutamise asemel normaliseerida. Kesksüsinikterastel (0,3…0,5 % C) on see erinevus suurem, mistõttu alati ei saa lõõmutamist asendada normaliseerimisega. Küll aga võidakse asendada nende teraste korral parendamine (karastamine järgneva kõrgnoolutusega) normaliseerimisega. Võrreldes lõõmutamisega annab normaliseerimine terasele suurema tugevuse, kuid võrreldes parendamisega on normaliseeritud teras mõnevõrra väiksema plastsuse ja sitkusega. Mittevastutusrikaste kergkoormatud detailide korral piirdutakse tavaliselt normaliseerimisega, vastutusrikaste raskkoormatud detailide korral aga tuleb eelistada parendamist. Normaliseerimise tulemusena muutub teras peeneteralisemaks, tugevus ja kõvadus on suurem kui lõõmutatud terasel. Normaliseerimist kasutatakse terase lõiketöödeldavuse parandamiseks ning sageli karastamise eeloperatsioonina. Üleeutektoidteraste (ka tsementiiditud teraste) normaliseerimisel kaob tsementiidi võrk.
Sferoidisatsioon
Kõrgsüsinikterased (> 0,6 % C), mille korral kasutatakse lõiketöötlemist, allutatakse sageli termotöötlusele, mis on tuntud sferoidisatsiooni ehk sferoidiseerimisena (spheroidizing) (vt ka p 4.2.1. Täislõõmutus). Siin on eesmärgiks saada terase struktuur, milles tsementiit on peeneteralisena feriitmaatriksis. See on saavutatav kas pikaajalise kuumutamisega temperatuuril alla A1 ja järgneva aeglase jahutamisega või pikaajalise tsüklilise kuumutamisega temperatuurivahemikus veidi alla A1, tööriistateraste (eelkõige kõrglegeerteraste) korral kuumutamisega temperatuuril 750…800 ºC ja pikaajalise seisutusega sellel, millele järgneb aeglane jahutamine. Eelkõige oleneb protsessitermotöötluse valik soovitavatest eesmärkidest, kusjuures määrav on terase keemiline koostis. Protsessitermotöötlustest piirdub lõõmutamine eelkõige madalsüsinikteraste, sferodiseerimine aga kõrgsüsinikterastega (üleeutektoidterastega). Normaliseerimist ja täislõõmutust kasutatakse nii ühtede kui teiste teraste korral. Samas saadab madalsüsinikteraste normaliseerimist omaduste ebaühtlus; kõrgsüsinikteraste korral, mil erinevad jahutuskiirused võimaldavad saada varieeruvaid omadusi, on aga eelistatavam täislõõmutus. Siit on süsinikteraste korral eelistatavamad termotöötlused järgmised: 0…0,4 % C – normalisatsioon;
Karastamine
Karastuseks ehk karastamiseks (hardening, quenching) nimetatakse termotöötluse protsessi/operatsiooni, mille tulemusel saadakse ebastabiilne (mittetasakaaluline) martensiitstruktuur. Eristatakse mitmeid karastusviise: läbikarastust (detaili kuumutamisega kogu ristlõike ulatuses) ja pindkarastust (kuumutatakse ainult pinnakihti); lauskarastust (jahutamisega kogu detaili ulatuses) ja kohtkarastust (jahutatakse detaili osa). Terase tavakarastus Tavakarastus ehk täiskarastus (full hardening) eeldab järgmisi etappe: terase kuumutamine üle faasipiiride A1 (üleeutektoidterased) või A3 (alaeutektoidterased), et tagada lähtestruktuuris vajaliku austeniidi teke; seisutamine sellel temperatuuril – austenitisatsioon, et tagada kogu detaili ulatuses mainitud temperatuurile vastava homogeense struktuuri teke; jahutamine kiirusega, mis on karastatava terase kriitilisest jahtumiskiirusest suurem, et vältida austeniidi laguproduktide (ferriidi ja tsementiidi) teket.
Kuumutus (heating)
Karastustemperatuuri (hardening temperature) valik. Teraste karastustemperatuur valitakse olenevalt faasipiiridest A1 ja A3. Mittelegeerteraste karastustemperatuuri valikul on aluseks lihtsustatud Fe-Fe3C faasidiagramm (faasidiagrammi teraste osa) (Joonis 4.10). Selle järgi võetakse alaeutektoidteraste (0,2…0,8 % C) karastustemperatuur tavaliselt 30…50 °C üle faasipiiri A3, üleeutektoidterastel (C > 0,8 %) 30…50 °C üle A1. Alaeutektoidteraste karastustemperatuuri valikul on lähtutud asjaolust, et nende teraste karastamisel üle faasipiiri A1, kuid alla faasipiiri A3 – s.o poolkarastus (non-full hardening) säilib struktuuris kõrvuti martensiidiga ka ferriit, mis vähendab terase kõvadust pärast karastust ja halvendab mehaanilisi omadusi pärast noolutust. Üleeutektoidterastel on seevastu optimaalne karastustemperatuur faasipiiride A1 ja Acm vahel, lähtudes kahest asjaolust: 1) karastades terast üle faasipiiri A1, säilib struktuuris martensiidi kõrval sekundaarne tsementiit, mis suurendab terase kõvadust; 2) kuumutades aga terast üle faasipiiri Acm, jääb struktuuri pärast karastamist märkimisväärne kogus jääkausteniiti. Sellise kuumutuse korral on ka austeniiditera suurenemise oht, mis omakorda põhjustab jämeteralise martensiidi teket ja karastatud terase haprumist, aga ka süsiniku väljapõlemist. Need asjaolud vähendavad terase saadavat kõvadust.
Kuumutuskiirus (heating rate).
Kuumutuskiirus on oluline temperatuuri ühtlustamise seisukohalt kogu ristlõike ulatuses ja sellega kaasneva struktuuri homogeniseerimisel. Kuumutuskiirusest oleneb eelkõige karastamise kestus, sellest aga omakorda protsessi maksumus, mistõttu kuumutuskiirust on otstarbekas suurendada. Kuumutamise kiirendamiseks on mitmesuguseid viise. Vedelkeskkondades (sula plii, sula keedusool) kuumeneb metall kiiremini kui gaasikeskkonnaga ahjudes. Ühtlane igakülgne detaili kuumutamine soodustab selle kiiremat kuumenemist. Kui detaili pinna kuumenemine oleneb ümbritsevast keskkonnast, siis edasine detaili läbikuumenemine sõltub ristlõikest ja terase soojusjuhtivusest. Kuumutuskeskkond (heating medium). Detaili kuumutamisel elektriahjus õhus või muus gaasilises keskkonnas leiab aset vastastikune keemiline reaktsioon metalli pinna ja ümbritseva keskkonna vahel, kusjuures olulised on kaks protsessi: 1) terase süsinikusisalduse vähenemine pinnakihis sealt süsiniku väljapõlemise tagajärjel (C + O2 o CO2); 2) terase oksüdeerimisel selle pinnal raudoksiidi ehk rauatagi teke (2Fe + O2 o 2FeO). Terase oksüdeerumine ja süsiniku väljapõlemine olenevad kuumutustemperatuurist ning -kestusest ja terase ning ümbritseva keskkonna koostisest. Kuna terase oksüdeerumine ja süsiniku väljapõlemine on difuussed protsessid, siis kiirenevad need eelkõige temperatuuri tõusuga. Ahju atmosfääris tekivad olenevalt keskkonnast mitmesugused gaasid (CO2, CO, O2, H2, H2O, N2, CH4 jt), mis mõjuvad terasele mitmeti. Nii vähendab H2 terase pinnakihi süsinikusisaldust, CO2 oksüdeerib, O2 ja H2O oksüdeerivad ja vähendavad süsinikusisaldust, CO ja CH4 suurendavad süsinikusisaldust. Terase termotöötlusel on vaja luua sellised tingimused, mille korral reaktsioonid oksüdeerumine l taandamine ja süsiniku väljapõlemine l süsinikuga rikastamine on tasakaalus, s.t terase pinnakihi koostis praktiliselt ei muutu ja metall ei reageeri keskkonnaga (s.t on neutraalne). Neutraalse keskkonna saamiseks ahjus on vaja, et oleks kindlas vahekorras süsinikusisaldust suurendavad oksüdeerivad ja süsinikusisaldust vähendavad taandavad gaasid olenevalt kuumutustemperatuurist ja terase süsinikusisaldusest, s.t oleks kindel suhe CO2/CO, H2O/H2, CH4/H2 jt vahel. Sel otstarbel kasutatakse kontrollitava keskkonnaga kuumutusahjudes nn helekarastuse (light hardening) korral vajaliku koostisega gaasisegude saamiseks eriseadmeid või oksüdeerumise ja süsiniku väljapõlemise vältimiseks kuumutamist sulades soolades (BaCl2, NaCl jt).
Jahutus (cooling)
Terase karastamisel on martensiitstruktuuri saamiseks vaja austeniit kiirelt alla jahutada martensiitmuutuse temperatuurideni, kuid mitte kogu temperatuurivahemikus (kuumutustemperatuurist toatemperatuurini), vaid temperatuurivahemikus 550…650 °C, kus austeniit on vähima stabiilsusega – ta laguneb suhteliselt kiiresti ferriidi ja tsementiidi eutektoidseguks. Lisaks temperatuurile oleneb austeniidi lagunemise kiirus ka terase koostisest. Nendest mõjuritest oleneb terase karastamisel kriitiline jahutuskiirus. Tempe ratuuridel üle 650 °C on väikestest allajahutusastmetest tingituna austeniidi lagunemise kiirus väike ja seetõttu võib terast selles temperatuurivahemikus jahutada aeglasemalt, kuid mitte nii aeglaselt, et leiaks aset austeniidi lagunemine. Vahemik 650…400 °C tuleb läbida kiiresti, kuna selles vahemikus on austeniit vähima stabiilsusega. Süsinikteraste korral algab allpool 400 °C uuesti austeniidi suhtelise stabiilsuse piirkond ning terast võib uuesti jahutada aeglasemalt (mõningate legeerteraste korral võib temperatuurivahemikus 400…300 °C austeniidi lagunemine kiireneda, mistõttu tuleb neid ka selles piirkonnas kiirelt jahutada). Martensiidi tekkepiirkonnas (alla 300…200 °C) on soovitatav terast jällegi sisepingete vältimiseks aeglaselt jahutada. Karastamise ideaalne jahutuskõver on toodud Joonisel .Eespool esitatust tulenevalt on oluline, millist mõju avaldavad jahutusvedelikud kahes temperatuurivahemikus:
- 550…650 °C, mil on soovitatav austeniidi kiire jahutamine selle lagunemise vältimiseks. Mida kiirem jahutus, seda rohkem tekib martensiiti ja seda suurem kõvadus saadakse;
- 200…300 °C, mil martensiidi tekkest tingituna on soovitatav aeglasem jahutus. Mida aeglasem on jahutus, seda väiksem on kalduvus karastuspingete ja pragude tekkele.
Jahtumiskiirus detaili ristlõikes oleneb ka detaili mõõtmetest: suuremad detailid jahtuvad aeglasemalt võrreldes väiksematega; südamik jahtub tunduvalt aeglasemalt kui pind. Nii võib juhtuda, et südamikus võib jahtumiskiirus osutuda väiksemaks kriitilisest (kiirus, millest väiksematel austeniit laguneb ja südamik ei karastu). Nii on see süsinikteraste (väikese läbikarastuvusega teraste) korral. Legeerterased on suurema läbikarastuvusega, kuna nendel on kriitiline jahtumiskiirus tunduvalt väiksem. Levinum jahutuskeskkond karastamisel on vesi. Vesi jahutab intensiivselt nii temperatuuripiirkonnas 650…550 °C (austeniidi lagunemine) kui ka temperatuurivahemikus 300…200 °C (martensiidi teke). Viimases peitubki vee kui karastuskeskkonna olulisem puudus. Õli jahutusvõime võrreldes veega on 3…4 korda väiksem temperatuuripiirkonnas 650…550 °C, kuid ca 10 korda väiksem martensiidi tekke piirkonnas. Õli kui karastuskeskkonna eeliseks on tema mittetundlikkus temperatuurile – õli jahutab ühesuguse intensiivsusega temperatuuril nii 20 °C kui ka 150…200 °C. Õli puuduseks on tema tuleohtlikkus (süttimistemperatuur sõltuvalt õli margist on 150…320 °C piires) ja karastusvõime kadumine aja jooksul (õli pakseneb). Peale selle õli põleb ja detaili pinnale moodustub oksiidikile. Vees lahustunud soolad või leelised suurendavad tunduvalt vee jahutusvõimet (temperatuuripiirkonnas 650…550 °C ligi 2 korda), mistõttu soolade ja leeliste vesilahuseid kasutatakse sageli jahutuskeskkondadena. Karastuspinged (hardening stresses, quenching stresses) Karastamisega kaasnevad terasdetailides sisepinged, mis liigitatakse lähtuvalt päritolust kahte rühma: ristlõike eri osade erinevast jahtumisest tingitud pinged (termopinged) ja faasimuutustest tingitud pinged (faasipinged). Termopinged ehk I liigi sisepinged (thermal stresses) on tsonaalsed sisepinged, mis tekivad ristlõike üksikute kihtide või detaili erinevate osade vahel. Mida suurem on termotöötlusel temperatuurigradient ristlõike ulatuses ja detaili üksikute osade vahel (see oleneb jahtumiskiirusest, jahutamise ebaühtlusest, detaili mõõtmetest ja tervest reast teistest põhjustest), seda suuremad on termopinged. Faasipinged ehk II liigi sisepinged (phase stresses) tekivad tera sisemuses või kõrvuti olevate terade vahel faasimuutuses osalevate faaside erinevast mahust. II liigi pinged ei olene ahtumiskiirusest, vaid eelkõige eri faaside mahtude erinevustest. Terase karastamisel tekkivad II liigi sisepinged on põhjustatud austeniidi ja martensiidi mahu erinevusest. See mahtude erinevus on seda suurem, mida suurem on terase süsinikusisaldus.
Karastusviisid
Karastusviisideks (hardening modes, quenching modes) olenevalt terase koostisest, detaili mõõtmetest ja kujust ning termotöödeldud detaililt nõutavaist omadustest tuleb valida optimaalne karastusviis, mis on kõige lihtsamini läbiviidav, kuid kindlustab ühtlasi ka vajalikud omadused. Mida keerukama kujuga on termotöödeldav detail, seda hoolikamalt tuleb valida jahutamistingimused, sest keerukamal detailil on tavaliselt suurem ristlõigete erinevus ning seda suuremad sisepinged tekivad tema jahutamisel. Mida rohkem sisaldab teras süsinikku, seda suurem on mahu muutus faasimuutustel, ning mida madalamal temperatuuril muutub austeniit martensiidiks, seda suurem on oht deformatsioonide, pragude, pingete ja teiste karastusdefektide tekkeks, s.t seda hoolikamalt peab valima terase jahutamisrežiimi. Tavakarastamisel kasutatakse põhiliste jahutuskeskkondadena vett, õli või kombineeritud moodust – läbi vee õlisse. Ühes keskkonnas karastus ehk vannkarastus (bath hardening, bath quenching) on lihtsamaid karastusviise. Vajaliku temperatuurini kuumutatud detail jahutatakse karastusvedelikus (vees või õlis) kuni täieliku mahajahtumiseni. Seda viisi kasutatakse süsinik- ja legeerterastest lihtsate detailide karastamisel. Süsinikterastest detailide läbimõõduga üle 5 mm karastusvedelikuks on vesi, väiksemate mõõtmetega detailide ja paljude legeerterastest detailide karastuskeskkonnaks on õli. Ühes vannis karastust kasutatakse eelkõige lihtsate detailide mehhaniseeritud karastamisel, kus detailid satuvad ahjust automaatselt karastusvedelikku. Keeruliste detailide karastamiseks kasutatakse teisi viise. Kahes keskkonnas karastuse ehk katkendkarastuse (time hardening, time quenching) korral jahutatakse detaili kahes keskkonnas – alguses kiirelt, seejärel aeglaselt jahutavas keskkonnas. Tavaliselt jahutatakse esmalt vees, et vältida austeniidi lagunemist, seejärel aga õlis või õhus, mis tagab detaili aeglase jahtumise martensiidi tekke piirkonnas. Sellist karastusviisi kasutatakse süsinikterastest tööriistade valmistamisel. Selle karastusviisi puuduseks on raskus kindlaks määrata ja reguleerida detaili seisutusaega esimeses keskkonnas, seda enam, et see aeg on väga lühike (mõõdetakse sekundites). See viis nõuab karastajalt küllaltki head kutseoskust. Astekarastus (stepped hardening, stepped quenching) on vaba katkendkarastusele omastest puudustest, mille korral detaili jahutatakse keskkonnas, mille temperatuur on antud terase martensiitmuutuse algtemperatuurist Ma kõrgem. Selles keskkonnas jahutamisel ja seisutamisel peab karastatav detail kogu ristlõike ulatuses omandama karastuskeskkonna temperatuuri. Sellele järgneb lõplik, tavaliselt aeglane jahutamine, mille jooksul tegelikult toimubki karastamine, s.t austeniidi muutumine martensiidiks. Selle karastusviisi korral tekivad minimaalsed sisepinged, sest jahutamine jaguneb kaheks etapiks. Karastuskeskkondadena kasutatakse sulasooli ja -leelisi (KNO3, NaNO2, KOH, NaOH) temperatuuriga 150…550 °C vastavalt astme temperatuurile. Astekarastuse kasutamine on piiratud detaili ristlõike teatud suurusega. Suhteliselt aeglaselt jahutavad keskkonnad ei võimalda saavutada suure ristlõikega detaili karastamise kriitilisi kiirusi. Seetõttu kasutatakse astekarastust eelkõige väikese läbimõõduga detailide korral: mittelegeerterasest detailid läbimõõduga 10…15 mm, legeerterasest detailid 20…30 mm. Isotermkarastuse (austempering, isothermal hardening, isothermal quenching) korral jahutatakse terast martensiitmuutuse temperatuurist Ma kõrgemal temperatuuril (250…350 °C) seisutusega kuni austeniidi lagunemiseni ferriidi ja tsementiidi seguks – beiniidiks (Joonis 4.12, kõver d) (vt p 4.3.1. Austeniidi lagunemine). Seetõttu on nimetatud karastusviis tuntud ka beiniitkarastusena.
Noolutamine
Terase karastamisel, mil austeniit muutub martensiidiks, saavutatakse suur kõvadus, mis on ka karastuse põhieesmärk. Ühelt poolt jahtumisel tekkivate termopingete ja martensiidi tekkest tingitud faasipingete olemasolu, teiselt poolt martensiidi suur kõvadus tingivad karastatud terase väikese vastupanu löökkoormustele ja deformatsioonidele. Neid omadusi aga on võimalik karastatud terase järgneva töötlusega – noolutusega ehk noolutamisega (tempering) – parandada. Saadavaks struktuuriks on noolutusmartensiit (tempered martensite). Noolutus on terase kuumutamine temperatuurideni alla A1, seisutamine sellel (vähemalt tunni) ja jahutamine (tavaliselt õhus). Madalatel temperatuuridel noolutus (200…250 °C) – madalnoolutus (low-temperature tempering) sobib eriti tööriistaterastele, millelt nõutakse suurt kõvadust, mis veel ei vähene järgneva kuumenemise (noolutuse) käigus. Noolutust temperatuuridel 300…400 qC nimetatakse kesknoolutuseks (middle-temperature tempering), mille tagajärjel tekkiv struktuur on küll veidi väiksema kõvadusega, aga väga elastne, mistõttu kasutatakse eelkõige vedrude ja ka näiteks puidutööriistade korral. Erinevalt tööriistaterastest (eesmärgiks on suurim võimalik kõvadus) püüeldakse konstruktsiooniteraste korral suurema sitkuse ja tugevuse poole. See saavutatakse suhteliselt kõrgetel temperatuuridel (450…650 °C) noolutuse – kõrgnoolutuse (hightemperature tempering) (450…650 °C) tulemusena. Sellist karastust koos järgneva kõrgnoolutusega nimetatakse parendamiseks (hardening and tempering). Terase mehaanilised omadused (kõvadus, tugevus, sitkus ja plastsus) muutuvad noolutustemperatuuri tõustes. Noolutustemperatuuri tõusuga vähenevad terase kõvadus, tõmbetugevus ja voolepiir, samal ajal aga paranevad terase plastsusnäitajad. Kõikide nende omaduste nõutav kompleks saavutatakse vastava noolutustemperatuuri valikuga. Lisaks sellele saadakse noolutamisel terase sobivam omaduste kompleks võrreldes austeniidi lagunemise tagajärjel saadud lamelse perliitstruktuurse terasega. Parendatud teraste voolepiir, väsimustugevus ja plastsus on tunduvalt paremad sama kõvadusega ferriitperliitstruktuursete teraste vastavatest omadustest. Eriti selgesti ilmnevad parendatud teraste eelised sitkusnäitajates eelkõige kõrgematel noolutustemperatuuridel. See seisneb peamiselt tunduvalt madalamas külmahaprusläves, millest allpool kalduvad terased haprale purunemisele. Parendatud terased ei kaldu haprale purunemisele tavalistel töötemperatuuridel. Nende eeliseks on ka suurem väsimustugevus, mis pole vähetähtis masinaosade korral. Parendamisel saadavad paremad mehaanilised omadused on tagatud juhul, kui terasel on pärast karastamist martensiitstruktuur kogu ristlõike ulatuses. Seega pole aluseta püüdlus väände- ja paindekoormusel töötavate detailide läbikarastuvusele. Parendatavate teraste süsinikusisaldus on 0,3…0,5 % piires. Kuna mittelegeerteraste läbikarastuvus pole eriti suur, määrab see eelkõige parendatavatest terastest detailide suhteliselt väikesed mõõtmed. Piiranguid pole suure läbikarastuvusega õlis karastatavatest legeerkonstruktsiooniterastest detailide mõõtmetele. Kasutatud materjal pärineb autoritelt Priit Kulu, Jakob Kübarsepp, Andres Laansoo, Renno Veinthal.